Ana Sayfa > S.S.S
S.S.S
Akdeniz Chemson’ın stabilizatör alanında yılların tecrübesine sahip olması sayesinde, üreticilerimize daha ekonomik çözümler sunabiliyoruz.
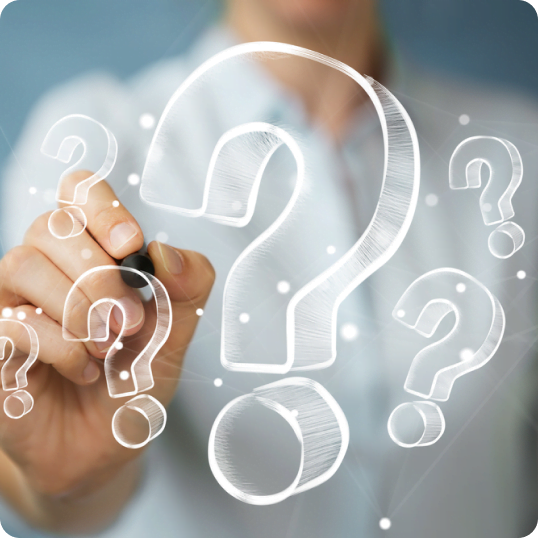
Nihai ürünün maruz kaldığı UV ışınlarının soğurulmasında görev alan ve örtücülük sağlayan beyaz pigment Titanyum dioksit tarafından ışınların kırılma indeksinin daha yüksek olduğu Rutil tip Titanyum dioksit kullanımı daha avantajlı olacaktır. Ayrıca, kablo uygulamalarında Anataz tip Titanyum dioksit kullanımında ürünün ilk renklenmesi daha iyi olacaktır.
Polimer yapıdaki PVC’nin zincir uzunluğunu ifade eden K değeri değiştikçe uygulama alanları da değişmektedir.
Esnek ürünler (kablo uygulamaları, hortum, suni deri, ayakkabı tabanı vb.) için K70-74 değerlerindeki PVC kullanımı önerilmektedir.
Kapı-pencere profilleri, esnek olmayan levhalar, dış cephe kaplamaları ve yağmur olukları vb. ürünler için K65-68 değer aralığındaki PVC kullanımı önerilmektedir.
Boru uygulamalarında; drenaj borusu üretimlerinde K58-67 değer aralığında, Atık su borusu için K65- 67 değer aralığında, temiz su borularında K67 ve üstündeki değerlerde PVC kullanımı son ürünün kalite testlerinde iyi sonuç alınması için kullanılmalıdır.
2mm’lik kenar bandı ve kablo kanalı benzeri ürünler için K63-65 değer aralığındaki PVC kullanımı önerilmektedir.
Profil uygulamalarında çoğunlukla ortalama tanecik boyutu 1 mikron civarındaki kaplı kalsit kullanılmaktadır. Kalsitin tanecik boyutunun yüksek olması, darbe dayanımını düşürmekle beraber mikser bıçakları ve ekstrüderin burgu-kovanında erken aşınmalar yaratacaktır. Kalsit, tanecik boyutunun çok düşük olması kuru toz karışımda topaklanma ve son ürün yüzeyinde izlere sebep olabilmektedir. Kalsitin tanecik boyutu kadar kaplama oranı da önemlidir. Kalsitin kaplama oranı, %0,7 ile %1,5 aralığında olmalıdır. Aşırı kaplama oranları, kalibratörde plate-out sorunu yaratabilmektedir.
Kalsit kullanım oranı yüksek olan uygulamalarda paralel burgulu ekstrüder yerine konik burguya sahip ekstrüder kullanımı daha avantajlı olacaktır. Konik burgular, tasarımı gereği ekstrüzyon sırasında malzemenin plastik olma süresini düşürecek ve yüksek miktardaki kalsit kullanılan karışımın daha kolay işlenmesini sağlayacaktır.
Mikserde homojen karışımı sağlanmış, nemi alınmış, akışı rahat bir toz karışım elde edebilmek için mikserin sıcak kazanında 5 ile 8 dakika sürecek şekilde 120 °C’ye kadar kademeli olarak pişirilen ham maddeler mikserin soğuk kazanında 40-50°C’ye kadar kademeli olarak 4 ile 5 dakika içinde soğutulmalıdır. Mikserde homojen bir karışım elde edebilmek için mikserin dolum oranı mikser kapasitesinin %75’i kadar hammadde ile dolu olmalıdır.
Mikser bıçakları uzun süreli kullanım ve yüksek kalsit miktarına bağlı olarak zamanla aşınır ve işlevsiz hale gelir. Eğer mikser süresi uzamaya başlamışsa, mikser prosesi sırasında amperde standarda göre artışlar varsa ve bıçaklar kontrol edildiğinde üzerlerinde karışım balçık gibi yapışıyor ya da aşınmalar belli oluyor ise bıçakların değişim zamanının geldiğini anlayabiliriz.
Akdeniz Chemson olarak ürettiğimiz akrilik yapıdaki proses yardımcılarından PRO-30, PRO-40 ve PRO-60 genel PVC uygulamalarında plastik olma süresini kısaltır, yüzey parlaklığına pozitif etki eder ve homojen bir eriyik akışı sağlar. Yüksek molekül ağırlığa sahip PRO-45 ve PRO-70 köpük uygulamalarında avantajlıdır. PRO-45 eriyiğin gaz tutma yeteneğini geliştirir bu sayede daha düşük yoğunluk ile daha homojen köpük elde edilmesini sağlar. PRO-70 malzemeye eriyik direnci sağlayarak ekstrüzyon sırasında oluşan köpük kabarcıklarının kalıp çıkışında basınçtan kurtulduğunda ürünün üst yüzeyine çıkışını engelleyerek effektif bir köpük katman oluşumu sağlamaktadır. PRO-50 kaydırıcılık özelliği de olan bir akrilik proses yardımcısıdır. PRO-50 kullanımı PVC eriyiklerinin sıcak metal yüzeylere yapışmaya yatkınlıklarını azaltır, kalıp kirlenmesini engeller, aynı zamanda nihai ürün için daha parlak bir yüzey sağlar.
Hammadde ve kuru karışımda bulunan nem ekstrüzyon öncesinde malzemenin akışını bozması ve topaklanma yaratmasının yanı sıra kalibratörde plate-out ve kalıp çıkışında sakal oluşmasına neden olacaktır. Bunu önlemek için PVC ve kalsit istenmeyen neme karşı kontrol edilmelidir. Mikserleme şartları (sıcaklık, amper) gözden geçirilerek optimum değerlerde çalışması sağlanmalıdır. Mikser aşamasında jet filtre kullanımı nemi azaltmak için etkili olacaktır.
PVC üretimlerinde kullanılan kaydırıcılar yapılan uygulama türlerine ve yapılarına göre proses değerlerine farklı etkiler gösterir. Genel tabiriyle Akdeniz Chemson bünyesinde üretilen kaydırıcılar, iç kaydırıcılar, dış kaydırıcılar ve oksitlenmiş polietilen kaydırıcılar olarak kullanılır. İç kaydırıcılar genel olarak tork ve basınç parametrelerinde büyük değişiklikler yapmazken, dış kaydırıcılar torku ve basıncı düşürür. Okside PE kaydırıcılar ise tam tersi etki yaparak ekstrüderin tork ve basınç parametrelerinde artış sağlar. Her bir kaydırıcının uygulama reçetesine göre kullanım oranı farklılık gösterir.
Kalsit (Kalsiyum Karbonat), PVC uygulamalarında 9 phr’a kadar nihai ürüne darbe mukavemeti verip pozitif etki yaratırken, 9 phr’dan fazla kullanımı malzemenin kırılma dayanımını düşürür. Ek olarak doğası gereği kalsit sarı renkli bir malzeme olduğundan nihai ürünün renk değerlerini değiştirir ve bu üretici firma için daha fazla pigment ve titanyum dioksit kullanması demektir. Kalsit, korozif bir malzeme olduğundan yüksek kalsit kullanımın kısa sürede toplam nihai ürünün toplam maliyetini düşürüyor gibi görünse de uzun sürede yüksek kalsit kullanımı, üretici firmanın gizli giderlerine (Burgu-kovan değişimi, mikser bıçakları değişimi, kalite problemleri kaynaklı müşteri şikayetleri) büyük etkisi bulunmaktadır. Diğer taraftan kalsitin yoğunluğu, PVC’nin yoğunluğundan büyük olduğundan metre ile satış yapan PVC profil üreticileri için malzemenin birim üretim fiyatını çok düşürmezken, kilogram ile satış yapan firmalara daha büyük maliyet düşüşü gösterir.
Darbe mukavemet arttırıcıların uygulama oranı PVC’den yapılan ürün tipine göre farklılık gösterir. Genel olarak müşterilerimiz, yüksek kalsit kullanılan PVC profil uygulamalarında darbe mukavemet arttırıcı ürünün uygulama formülünde girdisini arttırarak mukavemet problemlerini çözmeyi hedefleyebilmektedir. Darbe mukavemet arttırıcılar, PVC profil üretimlerinde optimum darbe mukavemet etkisi almak için 4 ile 7 phr arası kullanılır. 7 phr’dan fazla kullanımı malzemeye pozitif bir etki yaratmaz.
Bu konu reçete bileşenleri, ekipman ve stabilizatör ile ilgili kompleks bir durumdur. Akdeniz Chemson ile iletişime geçiniz.
Renklenmeyi sağlayan pigmentlerin UV direncinin yani güneş ışınlarına karşı bozunma direncinin yüksek olması uzun ömürlü bir son ürün elde edilmesinde oldukça faydalıdır. Bu özelliğin yüksek olduğu cool-color denilen ışık haslığı yüksek pigmentlerin kullanımı önerilmektedir. Ayrıca lamine kaplamalı ürünlerde yüzeyde laminasyon filmi olduğundan UV dayanımlı laminasyon filmleri kullanılmaktadır.